Oil Analysis
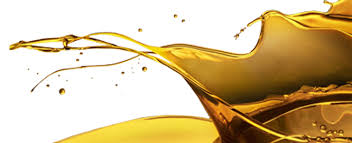
The first time, the Railway in the USA has done Oil Analysis of used Oil, in the early 1940s, for oil used in their locomotive engines.
Since then the tool ‘Oil Analysis’ in use and today it is one of the major tools (out of four) of Predictive Maintenance.
Lubricant/ Industrial Oil Analysis, Ferrography (Wear Particle/Debris Analysis), Particle Count Analysis & Transformer Oil Analysis are major testing methods. (Please refer the side strip for details of each)
Most of the machine catastrophic failures are avoided due to early detection of wear particles in gear oil through periodic monitoring of Oil condition.
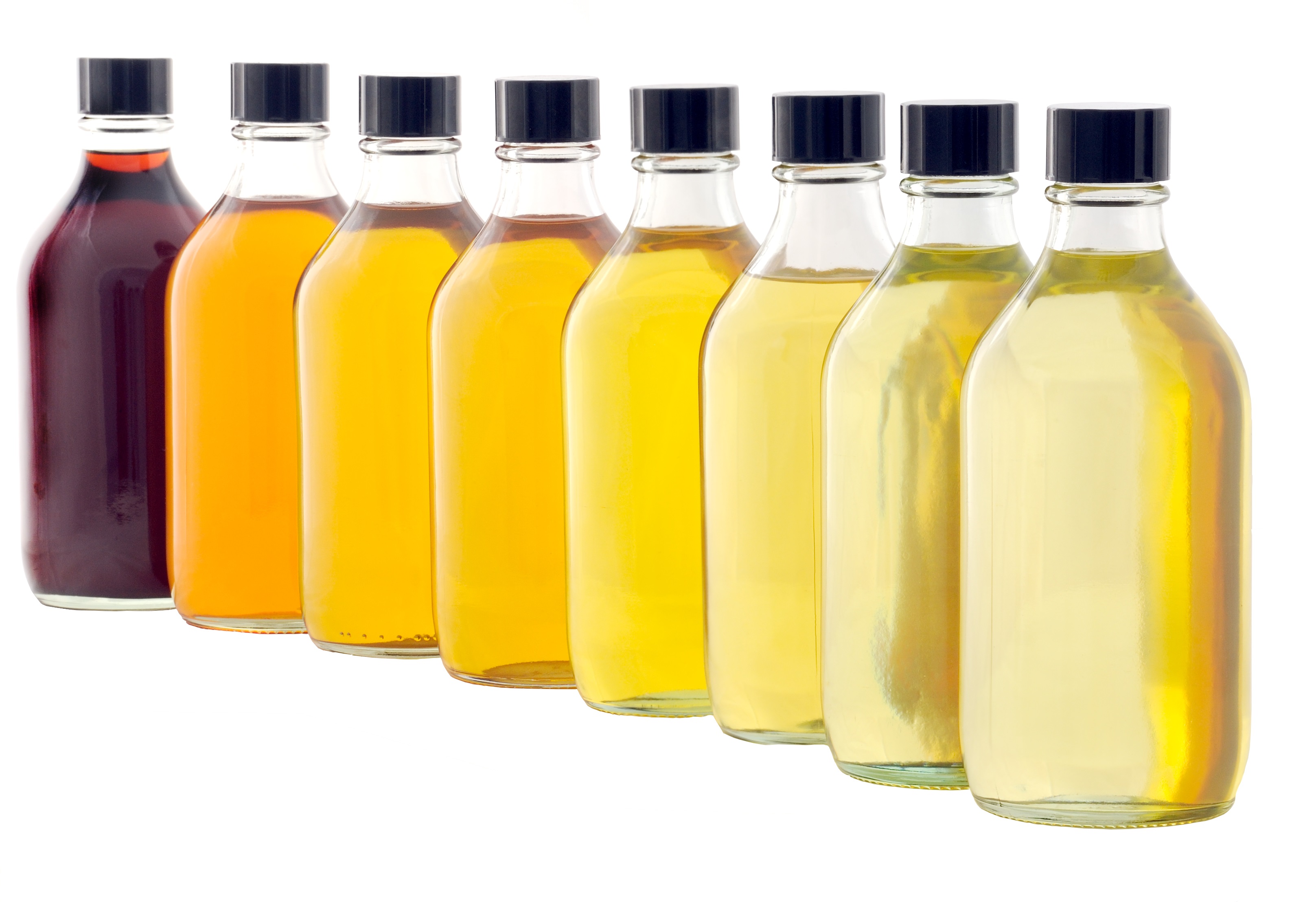
Why Test Oil?
Over 80% of equipment failures are contamination related breakdowns, oil analysis is one of the easiest ways to monitor contamination.
One of the keys to keeping machinery operating at optimal performance involves monitoring and analyzing lubricant oils for characteristics such as contamination, chemical content and viscosity.
Knowing how to interpret changing lubricant properties can increase both the uptime and the life of your mission-critical capital equipment. The existence or amount of debris and particles from wearing parts, erosion and contamination provide insights about the issues affecting performance and reliability.
Lubricant, fuel and other key fluid analyses provide critical early warning information indicative of machine failure. Analyzing and trending the data means you can schedule maintenance before a critical failure occurs. The result – higher equipment availability and productivity, lower maintenance costs, fewer outages, optimal equipment performance.
Different types of Testings' & their Usages
Colour Testing - Used to observe darkening of the oil by comparing it to previous samples of oil from the same transformer. Transformer oil colour is determined by means of transmitted light and given a numerical value (0-5) based on comparison with a series of colour standards. Noticeable darkening oil indicates either contamination or that arcing is taking place.
Dielectric Breakdown Voltage - Measures the voltage at which the oil fails electrically, which is indicative of the amount of contaminant (usually moisture) in the oil. The dielectric breakdown voltage is measured by applying a voltage between two electrodes under the oil. New oil should have a minimum dielectric strength of 35 kV by ASTM Transformer Oil Testing Methods.
Dissolve Gas Analysis (DGA) - Identifies various gas ppm levels that are present in transformer insulating oil. Different gasses will dissolve in the oil that indicates various types of thermal and electrical stress occurring within the transformer. An oil sample tube and the syringe is used to draw, retain and transport the oil sample in the same condition as it is inside a transformer with all fault gases dissolved in it.
Dissolve Metal Analysis - Identifies any dissolved metals that could originate from overheating or arcing and a portion of the particulate metals that may originate from mechanical wear. Measured by inductively coupled plasma ammonic emission spectrometry (ICP-AES) and expressed in micrometres.
Flash Point/ Fire Point - Indicates the volatility of insulating oil by measuring the minimum temperature at which the heated oil gives of sufficient vapour to form a flammable mixture with air.
Interfacial Tension - Measures the presence of soluble contaminants and oxidation products in transformer oil. Expressed in mN/m, it is a test of interfacial tension of water against oil, which is different from surface tension in that the surface of the water is in contact with oil instead of air. A decreasing value indicates an increase in contaminants and/or oxidation products within the oil.
Moisture (Water) Content - Measured in parts per million (ppm) using the weight of moisture divided by the weight of oil. Moisture content in oil lowers the insulating system dielectric strength and allows flashover that can damage a transformer. For mineral oil, generally accepted maximum moisture content is 35 ppm. This test does not measure the water content in the transformer paper insulation.
Neutralization (Acid) Number - New transformer oils contain practically no acids. The acidity test measures the content of acids formed by oxidation and contaminates. Measurements are made by the amount of potassium hydroxide (KOH in mg) required to neutralize the acid in one gram of oil. Typically, results of 0.10 mg KOH/gram of oil or less are considered good. Higher values are indicative of a problem.
Oxidation Inhibitor Content - Measures the amount of 2,6- di-tertiary -butyl par cresol and 2,6- di-tertiary -butyl phenol that has been added to new insulating oil as protection against oxidation. In used oil, it measures the amount remaining after oxidation has reduced its concentration.
Pour Point - Indicates the lowest temperature at which the insulating oil will flow. This test is particularly useful in cold climates to ensure that the oil will circulate and serve its purpose as an insulating and cooling medium.
Relative Density (Specific Gravity) - Determines the density, relative density (specific gravity), or API gravity of transformer oil by use of hydrometer at a reference temperature. A high specific gravity indicates the oil’s ability to suspend water. In extremely cold climates, specific gravity can be used to determine whether ice will float on the oil.
Resistivity - Measures the electrical insulating properties of transformer oil under conditions comparable to those of the test. A low resistivity reflects a high content of free ions and ion-forming particles in the insulating oil, and normally indicates a high concentration of conductive contaminants.
One of the keys to keeping machinery operating at optimal performance involves monitoring and analyzing lubricant oils for characteristics such as contamination, chemical content and viscosity.
Knowing how to interpret changing lubricant properties can increase both the uptime and the life of your mission-critical capital equipment. The existence or amount of debris and particles from wearing parts, erosion and contamination provide insights about the issues affecting performance and reliability.
Lubricant, fuel and other key fluid analyses provide critical early warning information indicative of machine failure. Analyzing and trending the data means you can schedule maintenance before a critical failure occurs. The result – higher equipment availability and productivity, lower maintenance costs, fewer outages, optimal equipment performance.
Different types of Testings' & their Usages
Colour Testing - Used to observe darkening of the oil by comparing it to previous samples of oil from the same transformer. Transformer oil colour is determined by means of transmitted light and given a numerical value (0-5) based on comparison with a series of colour standards. Noticeable darkening oil indicates either contamination or that arcing is taking place.
Dielectric Breakdown Voltage - Measures the voltage at which the oil fails electrically, which is indicative of the amount of contaminant (usually moisture) in the oil. The dielectric breakdown voltage is measured by applying a voltage between two electrodes under the oil. New oil should have a minimum dielectric strength of 35 kV by ASTM Transformer Oil Testing Methods.
Dissolve Gas Analysis (DGA) - Identifies various gas ppm levels that are present in transformer insulating oil. Different gasses will dissolve in the oil that indicates various types of thermal and electrical stress occurring within the transformer. An oil sample tube and the syringe is used to draw, retain and transport the oil sample in the same condition as it is inside a transformer with all fault gases dissolved in it.
Dissolve Metal Analysis - Identifies any dissolved metals that could originate from overheating or arcing and a portion of the particulate metals that may originate from mechanical wear. Measured by inductively coupled plasma ammonic emission spectrometry (ICP-AES) and expressed in micrometres.
Flash Point/ Fire Point - Indicates the volatility of insulating oil by measuring the minimum temperature at which the heated oil gives of sufficient vapour to form a flammable mixture with air.
Interfacial Tension - Measures the presence of soluble contaminants and oxidation products in transformer oil. Expressed in mN/m, it is a test of interfacial tension of water against oil, which is different from surface tension in that the surface of the water is in contact with oil instead of air. A decreasing value indicates an increase in contaminants and/or oxidation products within the oil.
Moisture (Water) Content - Measured in parts per million (ppm) using the weight of moisture divided by the weight of oil. Moisture content in oil lowers the insulating system dielectric strength and allows flashover that can damage a transformer. For mineral oil, generally accepted maximum moisture content is 35 ppm. This test does not measure the water content in the transformer paper insulation.
Neutralization (Acid) Number - New transformer oils contain practically no acids. The acidity test measures the content of acids formed by oxidation and contaminates. Measurements are made by the amount of potassium hydroxide (KOH in mg) required to neutralize the acid in one gram of oil. Typically, results of 0.10 mg KOH/gram of oil or less are considered good. Higher values are indicative of a problem.
Oxidation Inhibitor Content - Measures the amount of 2,6- di-tertiary -butyl par cresol and 2,6- di-tertiary -butyl phenol that has been added to new insulating oil as protection against oxidation. In used oil, it measures the amount remaining after oxidation has reduced its concentration.
Pour Point - Indicates the lowest temperature at which the insulating oil will flow. This test is particularly useful in cold climates to ensure that the oil will circulate and serve its purpose as an insulating and cooling medium.
Relative Density (Specific Gravity) - Determines the density, relative density (specific gravity), or API gravity of transformer oil by use of hydrometer at a reference temperature. A high specific gravity indicates the oil’s ability to suspend water. In extremely cold climates, specific gravity can be used to determine whether ice will float on the oil.
Resistivity - Measures the electrical insulating properties of transformer oil under conditions comparable to those of the test. A low resistivity reflects a high content of free ions and ion-forming particles in the insulating oil, and normally indicates a high concentration of conductive contaminants.